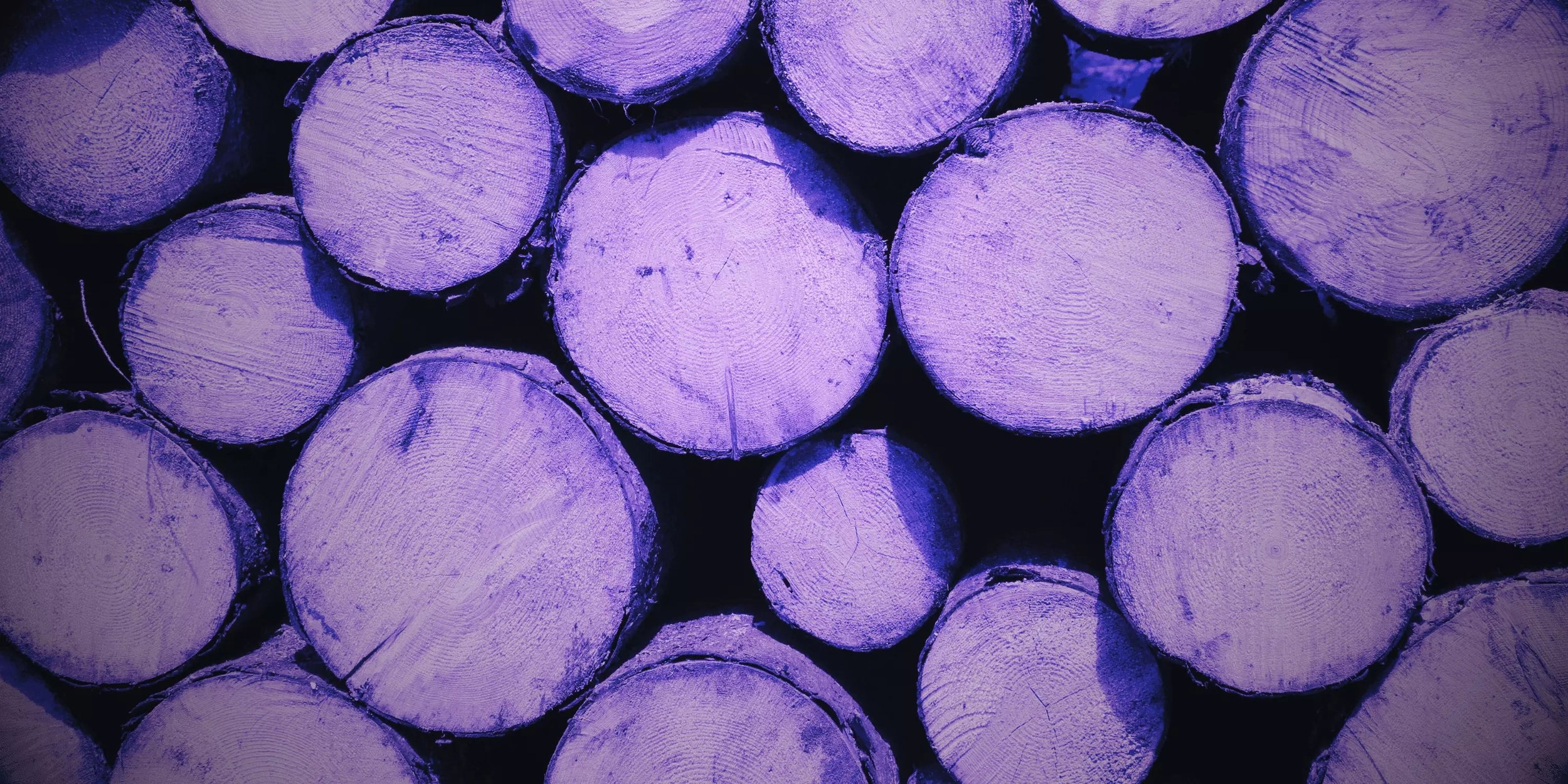
Wood & Furniture
-
Monitoring of the wood production process in real time through the control of machines, production lines and devices used in woodworking, in order to detect anomalies and intervene promptly.
-
Inventory management of raw materials, semi-finished products and finished products. Thanks to SkyMes it is possible to keep track of stocks of wood, components and parts, thus optimizing resource management and preventing interruptions in production due to lack of material.
-
Production planning by assigning priorities and resources and setting deadlines. This ensures all production cycles to be optimized and delivery times to be respected.
-
Quality control at every stage of the production process, helping to identify defects or anomalies in products in real time. This helps ensure that the finished products meet the required quality standards.
-
Total traceability of all products, allowing you to trace the history of each piece of wood or finished product. This is particularly important for ensuring regulatory compliance and responding to traceability requests from customers.
-
Optimization of energy and resources, reducing operating costs and environmental impact.
-
Data analysis and reporting to help you identify areas for improvement, reduce waste and increase the overall efficiency of the company.
-
Integration with any other software used by your company, such as workshop management systems, ERP systems and industrial automation systems, ensuring smooth communication between all company processes.